From Reliability to Electrification: Embracing Seal Gas Boosters for a Net Zero Future
January 9, 2025
10 Minute Read
In today’s fast-evolving energy landscape, the importance of deploying advanced decarbonisation-ready technologies cannot be overstated. Simply put, the time for action is now. The International Energy Agency (IEA) reinforces the urgency of adopting a future-minded strategy: "The next investment cycle could have an enormous impact on the trajectory of emissions from industry in the next three decades, and action is needed today to lay the groundwork for a smooth transition.”
Technologies that help improve plant efficiency are fundamental to emissions reduction efforts. One product within this category is the seal gas booster. Seal gas boosters are not only beneficial to compressor reliability, but can also help advance the broader electrification of industry — a movement that directly contributes to sustainability. This is especially the case when the power for electrically-driven seal gas boosters comes from renewable sources like solar and wind.
Keep reading to explore the key seal gas booster technologies available today and how they can support tangible net zero progress.
What is a Seal Gas Booster?
Seal gas boosters are part of a larger system that upholds compressor reliability; it comprises four main pieces of equipment, each with a distinctive function.
- The centrifugal compressor adds kinetic energy to process gas, increasing pressure.
- The dry gas seal enables a compressor shaft to rotate while helping minimise fugitive emissions to a negligible extent.
- The gas seal support system monitors dry gas seal performance and ensures that only conditioned seal gas reaches the dry gas seal during operation.
- The seal gas booster supplies clean, pressurised seal gas to the dry gas seal as needed to help uphold peak sealing performance.
A booster’s job is to provide the dry gas mechanical seal with a supply of clean, conditioned and pressurised seal gas when necessary. The dry gas seal needs this gas supply if, for example, a compressor is left on standby and there isn’t a sufficient flow rate for the primary gas buffer. A booster helps maintain the required flow rate while supporting other sustainability benefits.
Why are Seal Gas Boosters Essential?
A well-thought-out gas seal system is vital to efficient operating dry gas seals, which in turn are essential to centrifugal compressor performance. While boosters are not required for every application, their use is common to the oil and gas industry, for instance, when processing methane and other heavier gases like butane, propane and ethylene.
Boosters are part of a robust gas seal system and are specified in API 692: Dry Gas Sealing Systems for Axial, Centrifugal, and Rotary Screw Compressors and Expanders. The protocol states:
- Seal gas boosters are required unless the system design eliminates the conditions when needed; for example, when an alternate seal gas supply is available.
- A booster must operate when the process compressor is idle and pressurised or if the process compressor provides insufficient differential pressure.
- The booster shall be sized to provide normal seal gas flow for the range of all specified utility conditions.
As API 692 suggests, two main conditions require a booster:
- Settle out, or when the compressor is in a state of pressurised standby.
- Startup, or when there isn’t sufficient compressor pressure differential to run the seal.
In both cases, a seal gas booster will supply the dry gas mechanical seal until the compressor returns to ordinary operating conditions.
Besides supporting reliability, another reason to use a gas booster is to prevent particulates from entering and harming the dry gas seal, which can be a risk for new plants that are commissioning compressors and piping. Grit-like metal dust is often present inside new equipment; boosters are recommended during kickoff to help prevent issues like unwanted particle intrusion into the dry gas seal.
The use of seal gas boosters in today’s new energy compressor applications — including hydrogen compression/production and carbon capture sequestration — indicates the potential of boosters in future clean hydrogen production and carbon sequestering initiatives. By understanding the benefits of electric vs pneumatic boosters, operators can identify the right technology for their application, whether it involves hydrogen, CCUS or the processing of heavy gases.
Sustainability Features of Electric Boosters vs. Pneumatic Boosters
Beyond enabling operational efficiency, seal gas boosters can also play a role in sustainability — but not all technologies offer the same benefits. Take, for example, the two prevalent industrial booster types: pneumatically driven reciprocating boosters and electrically driven rotary boosters.
Pneumatic boosters are the more basic of the two technologies, while electrical-driven rotary boosters are the more advanced, reliable and widely adopted option. When comparing the features of these two devices, it becomes clear how each supports net zero goals.
Electric vs. Pneumatic Drive
The electrification of equipment has the potential to accelerate industrial decarbonisation. As electricity generation trends toward renewables, transitioning to electrically driven rotary boosters can ease carbon footprints and aid efforts to reach net zero.
The energy chain for pneumatic boosters is longer and therefore not as efficient as electrically driven equipment. A pneumatic system uses electricity to drive air, which boosts the process gas. For an electric system, electricity boosts process gas without any steps in between.
Rotary vs. Reciprocating Motion
The moving parts of electric rotary boosters have a smooth circular motion that’s continuous, stable and efficient; balanced with no wearing parts, a rotary booster’s lifespan reaches 24,000 hours. The magnetic coupling is hermetically sealed to prevent fugitive emissions between motor and booster without any need of a mechanical seal. This ongoing reliability helps reduce capital expenditures for replacement parts, thus conserving resources and promoting sustainability. They can function continuously for long periods without a redundant backup unit.
Pneumatic reciprocating boosters operate non-continuously like pistons that rocket back and forth in a linear fashion; this can lead to significant noise, vibration and wear on parts. Reciprocating boosters typically function for just 2,500 hours — a lifespan nearly an order of magnitude less than electrically driven rotating systems.
High vs. Low Efficiency
Electrically driven rotary gas boosters are more energy effective, as no leakage paths exist and the energy chain is shorter from electricity to compressed gas.
Pneumatic boosters require a long stretch of piping to bring in pressurised air, and the piping inevitably leaks air as it travels from the source of compression to the booster. There are also potential gas losses from the pneumatic booster itself, as its piston requires a continuous seal vent that wears, leaks and must route to a flare line without back pressure.
Encouraging Sustainable Investments
Seal gas boosters can bolster sustainability efforts by helping enhance the benefits of dry gas mechanical seals. Dry gas seals use significantly less energy than traditional wet mechanical seals, while supporting reliability and sealing effectiveness without the need for an oil lubrication system — just one reason why operators are choosing to retrofit from wet to dry gas seals.
Pairing dry gas seals with an electrically driven rotary seal gas booster helps prevent dry gas seal contamination and can boost reliability even further. This, in turn, supports operational efficiency and sustainability, especially compared with older wet seals and pneumatic gas booster technologies. A report from McKinsey & Company emphasises the urgency of turning away from fuel-driven systems toward electrification: "The sooner that site owners assess the potential to electrify, the more likely it is that they can choose the most practical moment to invest in electric equipment."
John Crane’s GCU Centrifugal Seal Gas Boosters
John Crane’s GCU Centrifugal Seal Gas Boosters enable industrial electrification and ensure that compressors have adequate pressure differential so that dry gas seals perform reliably even during startup or standby.
There are three ways to implement our boosters: as part of the gas seal support system, as a booster module and as a standalone product. All three of these implementations apply to first fit by an original manufacturer or to upgrades by an end user. John Crane engineers, thanks to several-decade experience in gas seal systems designing and manufacturing, can support customers with incorporating seal gas boosters into design or supporting retrofit of existing installations to replace obsolete and/or superseded technology.
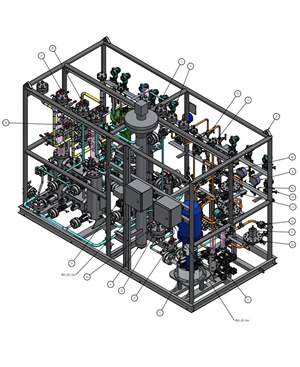
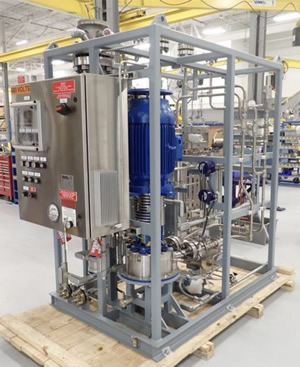
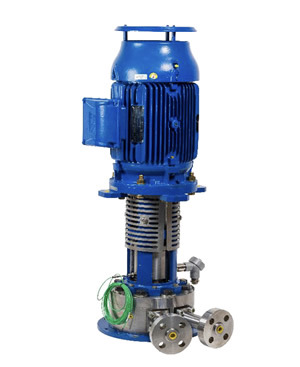
John Crane offers comprehensive turbomachinery solutions for centrifugal compressor manufacturers. Our extensive expertise and technology leadership allow us to support multiple aspects of dry gas seal design, including recommendations for gas seal support systems and booster units, along with maintenance and upgrade services via our network of local service centres.
A Net Zero Future Within Reach
In 1968, John Crane was awarded the patent for spiral groove sealing technology. We’re continuing this legacy in the new energy era by developing market-ready solutions that support industrial electrification, decarbonisation and the overall energy transition.
Our proven dry gas seals, gas seal support systems and boosters are continuously evolving to help our customers accelerate the path to net zero. Contact our experts for these and other innovations that enable your reliability and sustainability today.