Tackling the Hydrogen Embrittlement Challenge
June 27, 2024
7 Minute Read
As 2050 draws closer, hydrogen production is expanding rapidly. According to the International Energy Agency (IEA), the potential production by 2030 from announced projects to date is now 50% greater than at the release of its Global Hydrogen Review 2022. Acting quickly to enact hydrogen power is imperative from a carbon-reduction standpoint. However, accelerating the hydrogen economy is not without challenges — one of which is hydrogen embrittlement.
Hydrogen embrittlement, or when a metal loses ductility and becomes weaker due to hydrogen exposure, poses a significant threat to the structural integrity, thus to the service life of the equipment and machineries used in the new energy value chain. Keep reading for an introduction to hydrogen embrittlement, including the efforts that researchers are taking today to overcome its challenges and enable a sustainable future.
The Fundamentals of Hydrogen Embrittlement
Nearly 150 years ago, W.H. Johnson published a paper where he observed metals losing elasticity and becoming more brittle when subjected to hydrogen gas. He proposed a direct link between hydrogen exposure and decreased ductility in metals.
Modern research has deepened the scientific knowledge around Johnson’s findings, and today, metallurgists know much more about the mechanisms of embrittlement than Johnson did in 1875. But with many factors still not entirely understood, studies continue.
What is Hydrogen Embrittlement?
Hydrogen embrittlement, also called hydrogen-assisted cracking or hydrogen-induced cracking, is a problematic phenomenon. The heart of the problem is that a metal exposed to hydrogen atoms experiences increased brittleness and decreased load-bearing capacity, which causes parts to fail or break more quickly than expected.
Embrittlement stems from one of hydrogen’s unique physical properties. Its atoms are small — tiny enough to adsorb by dissolution and diffusion into a solid metal’s microstructure. Once they do, they detrimentally alter material characteristics and mechanical behavior, either causing the initiation of cracks at stresses below a metal’s projected yield strength or locally yielding and necking.
Hydrogen embrittlement is gaining significant attention now that the world is looking for clean energy from hydrogen because much of the value chain relies on equipment that is susceptible to this problem.
How Hydrogen Embrittlement Causes Metal Failure
Hydrogen-related cracking is difficult to predict in real-world scenarios. However, we do know that four basic conditions must exist for embrittlement to become a risk:
- There must be a susceptible material
- With exposure to hydrogen gas
- Experiencing tensile stress
- Relatively low temperature, below 150°C
Embrittlement begins in metals at the microstructural level. Hydrogen atoms are the smallest known to science. They are light and move quickly compared to the atoms of other elements. When introduced onto a metal’s surface, hydrogen diffuses into the metal itself, infiltrating and compromising the grain structure. The configuration of a metal’s grain structure — or its microstructure — is what grants physical properties like hardness, strength, toughness and corrosion resistance.
Once absorbed, the tiny hydrogen atoms accumulate in locations with available space, typically at grain boundaries. The build-up of atoms creates an internal pressure that increases the likelihood of cracks when the metal is subjected to stress.
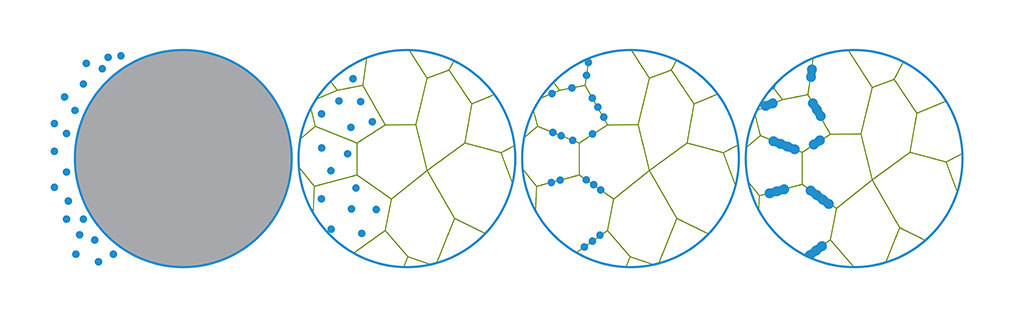
Ironically, high-strength steels are particularly susceptible to embrittlement. These types of metals are sensitive to the pressure inside their microstructure because of their stiffness. They crack more easily when exposed to hydrogen compared to softer, ductile metals.
Permeation of hydrogen in metal alloys increases at elevated temperatures as both the diffusivity and the solubility increase. However, embrittlement most likely occurs at approximately the room temperature range, where the interaction between hydrogen atoms and structural defects such as vacancies, dislocations, grain boundaries and incoherent interfaces are stronger. Most metal alloys are considered immune to hydrogen embrittlement at temperatures above 150°C, where other deformation mechanisms such as creep, are rather effective. Thermal cycling between room temperature and high temperature may exacerbate embrittlement, as a large amount of hydrogen charged at a high temperature can cause supersaturation in metal alloys and fast crack growth rates at room temperature. Because of this, hydrogen embrittlement is also called “cold cracking.”
Another factor that influences embrittlement is metal quality. Unsuitable production processing, heat treatment and manufacturing operations can diminish a metal’s purity, imparting inclusions or defects into a metal’s microstructure. These voids are a preferential space for hydrogen atoms to accumulate and induce cracking.
For industries transitioning to hydrogen, such as power generation, long-haul transportation and chemical production, addressing embrittlement is a priority as they integrate new, cleaner energy sources into their energy mix.
How Hydrogen Embrittlement Challenges the Hydrogen Economy
Hydrogen has the potential to support global energy needs. Yet before a full-scale adoption takes place, researchers must establish how hydrogen embrittlement influences each link in the value chain. Doing so can help quantify the risks and solve this critical problem.
Hydrogen Transportation
Transmission pipelines are a promising option for moving hydrogen along the value chain. Leveraging the world’s existing network of natural gas pipelines may be possible; however, the risk of hydrogen embrittlement requires consideration.
From a pipeline transportation perspective, two key challenges restrict the development of the hydrogen economy:
- Materials: There are currently no known ideal materials for hydrogen pipelines. Developing a piping solution that’s hydrogen embrittlement resistant, high strength and low cost would accelerate the transition to hydrogen energy.
- Standardized testing: A controlled method for assessing hydrogen embrittlement in pipeline steel is needed. A reliable approach for testing pipe and fittings is vital to ensure public safety and the integrity of transmission networks.
Hydrogen Storage Systems
Safe, large-scale storage systems will be essential as the hydrogen economy matures. Two options for storing pure hydrogen include compressed gas and liquid.
A compressed gas solution requires high-pressure tanks to counter hydrogen’s low volumetric density. However, high-pressure storage increases the risk of metal embrittlement. Using stable austenitic stainless steel and hydrogen-resistant liners are the leading methods for defending against embrittlement. Still, more research is necessary to define the service lifespan of compressed gas storage tanks and their associated components.
Liquified hydrogen storage requires extremely cold conditions. The inversion temperature of hydrogen is -71°C, above which the gas heats up on expansion due to a negative Joule-Thomson coefficient. During operations, there can be thermal swings as the cold liquid at about -253°C passes through ambient-temperature valves, causing the hydrogen to evaporate into a gas. This may expose valves and other metal components to hydrogen atoms, creating a mechanism for embrittlement.
Some material structures, such as Body-Centered Cubic (BCC), present ductile-to-brittle transition when cooled below room temperature. In these cases, materials used for storage and refueling devices can fail due to either of the two issues.
End-Use Applications
The majority of hydrogen use today is in refining, ammonia production and chemical production. Moving forward, the applications for clean hydrogen as an energy carrier abound. This potential includes industries that require heat energy combustion, where hydrogen is being considered as a replacement for coal and natural gas, both of which emit carbon. However, it requires a detailed understanding of combustion characteristics to evaluate the risk of embrittlement when burning hydrogen for energy (either for power generation or heating).
Consider steel and concrete production, as examples; both industries could theoretically replace fossil fuels with hydrogen or hydrogen-gas blends, yet each application has unique variables like temperature, furnace component geometry, metal composition and operational pressures. All these factors alter the way embrittlement is known to affect metal. Hydrogen direct reduced iron processes have now reached production phases in many countries to replace carbon and gas reduction methods in steel making.
Application-specific evaluation is necessary to determine whether an end-use process is appropriate for hydrogen. From fuel cells to home heating to industrialized processing, hydrogen’s use varies greatly across different applications. The lack of standardized, repeatable assessment is a stumbling block to accelerating hydrogen adoption.
It’s imperative to develop economic strategies that ensure safety for every link in the hydrogen value chain. The conversion to new energy will require extensive research aimed at understanding, predicting and mitigating the embrittlement of steels.
Efforts to Address Hydrogen Embrittlement
Despite considerable research into the mechanisms of failure and the development of potential mitigating solutions, the challenges presented by hydrogen embrittlement are not fully solved. Fortunately, exciting pilot programs and academic research are generating insights that could topple many obstacles in the coming years.
Materials Selection
With few metals suitable for hydrogen gas environments, embrittlement has the potential to slow the hydrogen economy’s growth. To bridge this gap, many researchers are developing modern embrittlement-resistant materials with high strength. Research groups, universities and industries across the globe are researching materials appropriate for hydrogen service. Meanwhile, scientists have found potential in specialized high-entropy alloys, which have demonstrated excellent hydrogen resistance.
Component Testing
Currently, ASTM F519 sets out a standard mechanical test method for hydrogen embrittlement evaluation, which requires sacrificial test specimens. However, destructive, laboratory-driven assessment is not practical in many industrial situations.
Non-destructive testing (NDT) methods for embrittlement are more applicable to in-field work environments and retrofits. Some NDT approaches in development include ultrasonic testing, radiography, eddy current testing and magnetic particle inspection.
Barrier Coatings
Since the discovery that surface treatments such as electro-polishing and fusion welding (when it is a surface process) can potentially accelerate hydrogen embrittlement, there have been ongoing efforts to thwart the ingress of hydrogen atoms into metals. For example, researchers have identified several ceramic-based barrier coatings and alloy structures with the potential to delay, reduce or prevent hydrogen absorption into metal.
Innovative Solutions for the New Hydrogen Value Chain
From embrittlement to intermittency, hydrogen production and handling pose numerous challenges for global operators. John Crane is committed to developing innovative technologies that address these challenges, empowering our customers to shape their new energy reality today. Our multidisciplinary teams are working to develop novel parts for the extreme conditions of stress, temperature and cycling loading encountered in the hydrogen value chain.
Explore our market-ready hydrogen solutions and contact our experts for help accelerating your energy transition.