Water Waste Reduction in Pulp & Paper Mills
Part 2: Four Additional Strategies to Improve Pump Reliability
December 15, 2023
5 Minute Read
By 2030, the global population is projected to reach 8.5 billion, emphasizing the urgent need to safeguard essential resources, with water conservation paramount. According to the United Nations, approximately 40% of the population is currently impacted by water scarcity, underscoring its substantial importance and growing concern.
In part 1 of this series, we introduced four initial strategies on how to reduce wastewater and enhance pump reliability in pulp and paper mills. We continue with four additional strategies:
- Use smart water control systems that reduce up to 97% of water consumption compared to the water savings produced by once-through metered flushes. These control systems regulate water consumption based on seal temperature, only allowing seal water to flow through the system when needed to cool the seal. Unlike flow meters, where the seal water runs through the system once and drains, smart water control systems, such as the John Crane Smartflow— suitable for dual seals, recirculate the same water multiple times in a closed loop, only adding water when needed, further reducing water consumption.
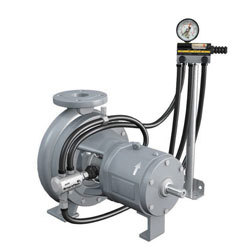
- Optimize your pumps using dual mechanical seals paired with a seal support system, such as a pressurized water vessel to extend the life of the mechanical seal as it is running in its own clean environment. This approach reduces water consumption in the event of a seal failure where only the water in the seal support system is lost, which typically equates to just eight litres.
- Further optimize your pumps by selecting dual mechanical seals with enhanced seal face technology. Sophisticated and simple dual seal solutions can reduce water consumption to nearly 1/100 of single seal requirements by applying advanced, self-pressurizing seal face technologies, such as John Crane’s Upstream Pumping (USP) technology. Where pumps move fluids high in solids or low in lubricity, USP spiral grooves use a small measure of clean seal water to pressurize and lubricate the faces in contact with the process fluid (Figure 1). These spiral grooves, normally seen on compressor gas seals, draw in the clean seal water and pressurize it as the water is forced into the tips of the grooves. The pressure at the groove tips causes the faces to ‘lift off’ and run without any contact and push a small quantity of the seal water into the pump, without needing to provide the seal water at a higher pressure than the stuffing box pressure.
Figure 1. Spiral grooves distribute water over the non-contacting seal face
By running on the clean seal water without the need for a continual flush, and only consuming a very small quantity, water consumption is greatly reduced, while also providing the benefit of low wear and high reliability in the harshest environments such as harmful solids or corrosive process liquids. Being able to operate even when the seal water pressure is much lower than the stuffing box pressure (seal water pressure typically around 0.2 bar g / 3 psi g) means that a simpler water supply system can be used, and the need for water pressure boosters on high-pressure pumps is eliminated.
Another quick, easy, and cost-effective solution to enhance mechanical seals and enable reduced seal water consumption is upgrading the seal face materials. Specifically, upgrading to John Crane Diamond® seal face technology offers numerous features and benefits derived from the exceptional properties of pure diamond. Notably, the low coefficient of friction achieved with Diamond seal faces allows for cooler seal operation, reducing the reliance on cooling water.
John Crane Diamond
In certain applications, this can result in up to a 70% reduction in heat generation, consequently leading to a substantial reduction of up to 70% in cooling water requirements. Some cases in higher-duty applications have shown potential savings of up to 2 million gallons per year in cooling water usage. Considering even a conservative cost of $0.0025 per gallon of water, this equates to annual savings of $5,000, plus the additional benefits of reduced wastewater costs.
For more information about how this works in practice, check out these resources on our website.
Partner with Experts
Seals play a vital role in the efficiency of pulp and paper operations, with factors like packing, and single or dual mechanical seals significantly impacting various aspects. At John Crane, we have the knowledge and experience to assist you in choosing the appropriate seals, enabling substantial water savings amounting to millions of gallons. Reducing water consumption can also minimize associated costs and environmental consequences.
Contact us today to learn more about John Crane's comprehensive range of products, services and training opportunities tailored for the pulp and paper industry.
Note: This content was featured in the PITA journal Paper Technology International®
Keep Exploring
To further enhance your knowledge, here is a selection of related resources. Whether you're looking for insightful videos or informative webinars and brochures, keep exploring and discover more.
Webinars and Brochures
Water savings: Discover innovative strategies for conserving water.
Smartflow: Get detailed insights on the Smartflow system and its benefits.
Case Study
Upstream Pumping: Learn from real-world applications and successes.
Videos
Upstream Pumping: See seal face technology in action.
John Crane Diamond: Explore the innovation behind this seal face technology.
Blog
Upstream Pumping: Learn how USP improves the total running cost of mechanical seals.