Upstream Pumping Improves the Total Running Cost of Mechanical Seals
April 4, 2023
10 Minute Read
How Upstream Pumping Technology Works
Upstream Pumping (USP) is a seal face technology unique to John Crane, which adds the spiral grooves, commonly seen in non-contacting gas seals, to the inboard seal of a dual mechanical seal running on a liquid barrier fluid. The grooves draw in the barrier fluid and pressurize it as it reaches the tips of the grooves. This pressurization has the combined effect of causing the seal faces to ‘lift off’ each other, running with zero contact, and it can cause a low-pressure barrier fluid to leak backward by being pushed into a high-pressure process stream.
More information on this novel technology, including a video showing the operation of the spiral grooves, can be found here.
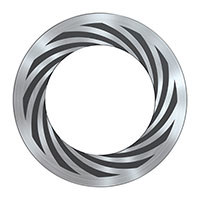
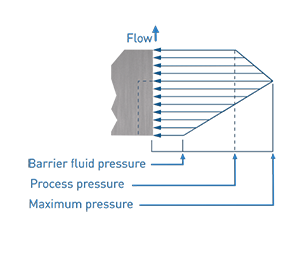
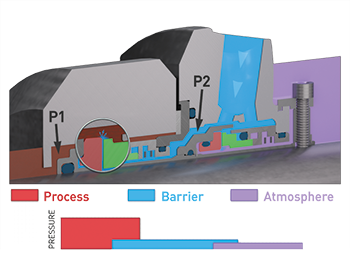
The non-contacting seal face and unique pumping technology create several benefits for the operator of these seals.
No Flush Required
Mechanical seals have friction between the rotating and stationary seal faces. This friction generates heat that must be removed from the seal area. This is traditionally done by inducing a flow of fluid over the seal faces. The simplest and most common way to achieve this is to flush the seal chamber with a continuous flow of clean fluid. This could be a small amount of the pump process fluid that has been routed back to the seal chamber from a higher-pressure line, or an external supply of clean fluid may be flushed directly into the seal chamber.
For abrasive or slurry services, suspended solids must be kept away from the seal faces. This is another reason that an external clean flush may be required at a flow rate high enough to expel solids from the seal chamber.
The non-contacting inboard faces of a USP seal operate with much less friction. With much less heat to be removed, a seal chamber flush is not required.
In addition, the leakage profile of USP seals allows them to be constructed in a face-to-back arrangement where the sensitive seal components are isolated from the process fluid. The faces are lubricated by the clean barrier fluid, so there is no concern about the abrasives damaging the seal faces. Therefore, no seal chamber flush is required.
Eliminating a continuous external seal flush saves a significant amount of fluid being injected into the pump. A typical seal might consume up to two gallons(10 liters) of fluid per minute. Even with a less expensive fluid such as recycled water, where the main cost is pumping and treatment, eliminating a seal flush can save thousands of dollars per seal per year. If the flushed fluid is more expensive, such as mineral oil, eliminating this flush can result in even greater savings.
Lower Heat Generation
On dual mechanical seals, the heat generated by the friction from the seal faces must be removed even if there is no seal flush present. This is normally achieved by circulating the barrier fluid through a heat exchanger, which must be properly sized to remove all the heat entering the barrier fluid at the seal. With traditional seals, the use of a water-cooled heat exchanger can be common due to the higher heat loads.
The non-contacting inboard faces of a USP seal operate with much less friction, therefore there is much less heat to be removed. This reduced heat load means that much smaller coolers will be required. This will often mean that an air-cooled heat exchanger may be used in situations where a traditional seal may have required a water-cooled heat exchanger.
Changing to a smaller heat exchanger avoids the initial setup cost of purchasing a larger cooler. If a water cooler can be eliminated, this avoids the water cost of running a water cooler.
Each water cooler uses at least 1.75 gallons(eight liters) per minute of water which can incur over $2,000 per seal, per year in water costs.
Lower Motor Friction
When mechanical seals generate heat from friction, the heat energy is absorbed from the power of the motor driving the pump.
The non-contacting inboard faces of a USP seal operate with much less friction, therefore less power is absorbed from the motor.
This increases overall skid efficiency and reduces electrical costs. In Europe, the legislative trend is towards rating the overall efficiency of the entire skid instead of rating the pump and motor separately.
Extends Seal Life
When mechanical seal faces run against each other, friction causes wear on the faces. The amount of friction determines the rate of wear and, accordingly, the maximum operational life of the mechanical seal.
For a continuously running USP seal, the inboard seal runs with zero contact and, consequently, zero wear. All wear to the inboard seal occurs from the wear during stop/start operations, and the grooves may become less effective over time if the water contains contaminants that clog or erode the groove profiles. Otherwise, the inboard faces would have a theoretically infinite life, and the life of the seal will be set by the wear of the outboard seal. The outboard seal is running with a small pressure differential due to the low-pressure barrier fluid, and hence they also have long lives.
The typical life for a USP seal is at least five years, and it is common for USP seals to have a life of up to or over ten years.
This increased mean time between repair (MTBR) saves on seal repair costs and minimizes downtime if a condition-based maintenance regime is used.
Seal Resilience to Service Conditions
USP seals are much more resistant to difficult service conditions and operational upsets, which could quickly damage traditional mechanical seals, causing short and unpredictable life, such as abrasive damage, low lubricity and pressure pulsations. As there are conditions that would normally cause severe damage to a traditional mechanical seal, which a USP seal is extremely robust against or even completely immune to, it means that they have been successfully deployed as ‘problem solver’ seals on bad actor pumps with very short seal life. For more detailed information on this topic, read our blog post on this topic.
If a site includes a pump where the seals are being damaged after only months or weeks of running due to one or more of these forms of damage, switching to a USP seal could completely change the story and eliminate the reliability issue. This would lead to increased uptime and a predictable process stream.
Simple System
Like other dual seals, a USP seal requires a support system to function properly. However, the needs of a USP seal are much simpler than a traditional seal. Therefore, the support system can be a much simpler design which is only required to supply a low-pressure barrier fluid and replenish fluid which is pumped across the inboard seal faces. This simpler, low-pressure support system may lead to a lower initial purchase cost compared to a traditional system for a dual mechanical seal.
The most used barrier fluid for a USP seal is water. This is because low-pressure water is usually readily available at the pump location, and many services which are ideal for USP technology are also compatible with a small amount of water being injected into the process stream. Therefore, USP support systems are normally designed to be connected directly to the site water supply. This means that they will automatically replenish barrier water as it is consumed, and there is no need for regular top-up activities from site maintenance personnel. The operation is much simpler than most common types of dual-seal support systems.
The GS USP is John Crane’s globally standardized USP support system. It is designed to fit directly into the site water supply, has a small footprint and is easy to install and operate.
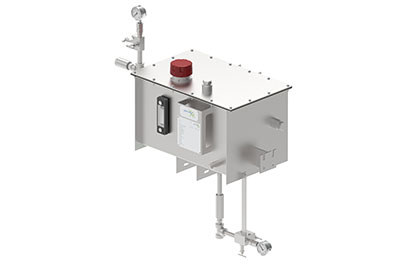
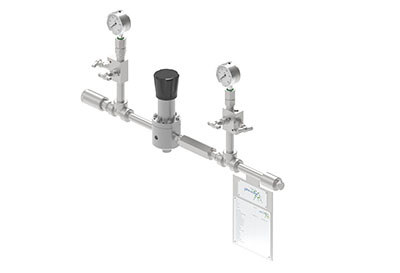
Total Cost of Ownership
Adding USP seal face technology to mechanical seals reduces costs by eliminating the need for a flush and/or water cooler, extending MTBR, and reducing power requirements. Combining these factors with simplified support system requirements and the resulting lower maintenance costs generates a benefit to operators of this unique technology.
The example below shows a cost comparison between a traditional seal and one using USP seal face technology. The increase in the MTBR of the seal, along with the reduction in water consumption and power usage, results in a maximum cost savings of up to $3,910 per seal, per year.
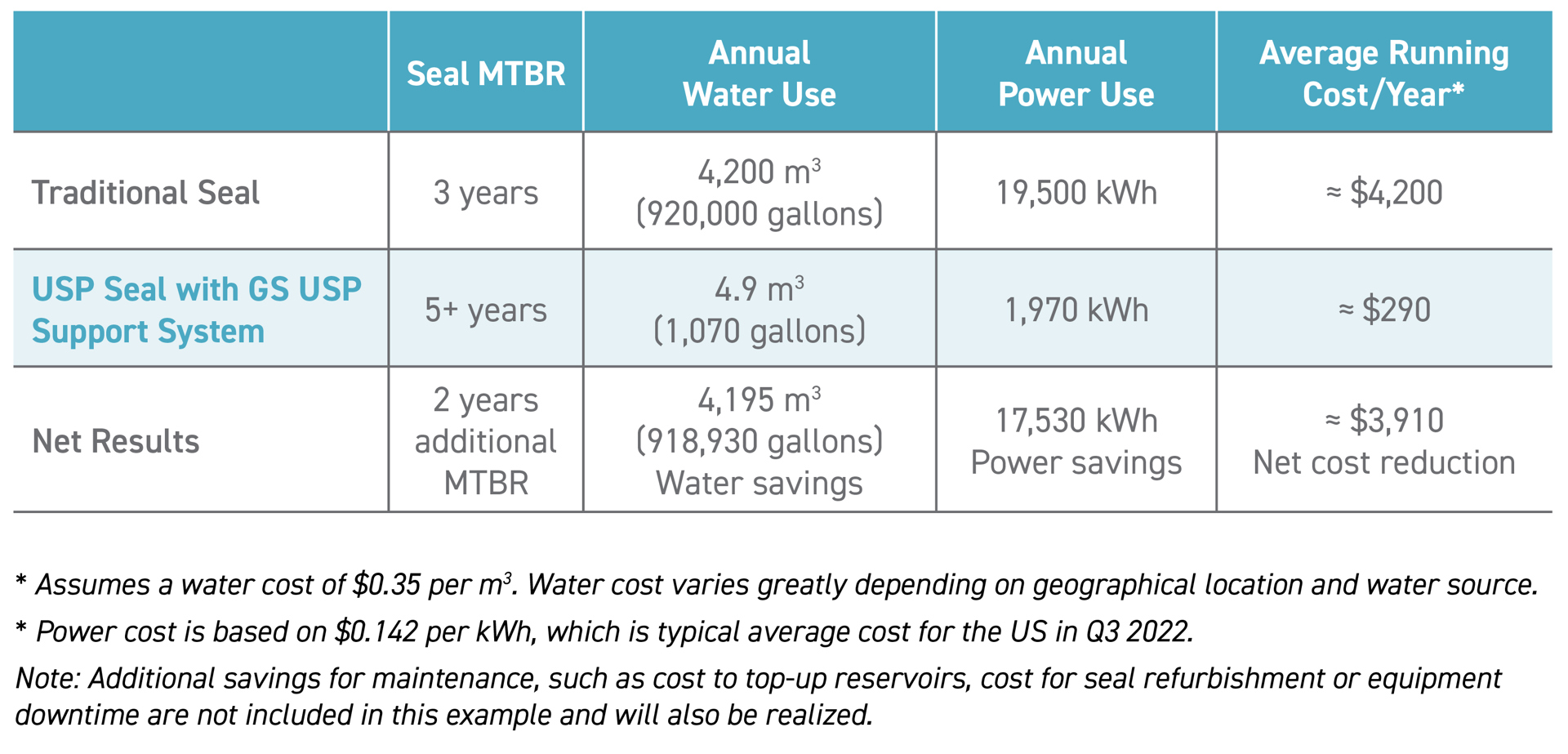
Partner with USP seal face technology experts
Are you ready to learn more about the benefits of using Upstream Pumping seal face technology? At John Crane, we have over 100 years of experience, so contact one of our experts today.