Converting Condition Monitoring Into Effective Condition-Based Maintenance Subhead: Part 1: Condition Monitoring Versus Condition-Based Maintenance—Definitions and Benefits
March 28, 2023
4 Minute Read

Condition Monitoring (CM) and Condition Based Maintenance (CBM) may look similar and are often used interchangeably, however, these two aspects of maximizing plant uptime and reducing risk are different. We have created a five-part series to help you learn more about CM and CBM and their essential role in helping you increase plant production, reduce maintenance costs and lower the total cost of ownership.
Condition Monitoring Versus Condition-Based Maintenance
CM is a range of activities undertaken to determine the condition of an asset. Correctly applied, this supports the identification of faults ahead of failures.
On the other hand, CBM is the act of maintaining equipment based on its condition and is dependent on effective CM. CBM should be applied strategically to ensure that the correct techniques are used on the proper schedule and to ensure the measurements are correctly set up.
Where technically and economically feasible, CBM strategies offer the lowest lifecycle cost by maximizing plant uptime and reducing risk.
Strategy
A strategic mix of reactive, time-based and CBM is typically applied across a plant. Determining the strategy is generally based on the asset register, the criticality of the machines, the failure modes and the detectability of those failure modes.
No matter how detailed the analysis used in the strategy assignment, data feedback from the operation is a necessary part of the control loop on the management controls. This enables the program manager to either keep doing what works or make a change. The types of changes and the measures are discussed in this educational series as “management controls.”
CM can involve combining techniques, including observations from operator rounds, lubricant analysis and performance monitoring. Whatever method is selected must be technically feasible, detect the failure modes to be defended against, meet the organization’s requirements and be economically justified. If it does not do that, the strategy must be revisited. For example, when an unexpected failure occurs, it is vital to examine the following:
- Was it detected?
- Could it have been detected with different techniques?
- Was the correct strategy applied?
- If it was detected, why wasn’t it addressed?
CBM Program Benefits
CM should form part of a continuous improvement engine. The business can manage these things by measuring key machinery conditions and operations indicators. An effective CBM program should be used to support reliability improvement and can help the site team to:
- Minimize the downtime of equipment to avoid exposure to the risk of plant downtime
- Prioritize the maintenance of assets
- Manage its spares
- Ensure each unit runs to its fullest expectable Mean Time Between Overhauls (MTBO). Rotating equipment should be expected to require “routine” maintenance such as oil freshening/replenishment, bearing replacements and alignment checks within its MTBO lifecycle
- Assist in assessing realistic expectable MTBOs instead of a generic five-year service life. This can also assist in managing the runtime of machines and avoiding preferential running of specific units over their sister units
- Eliminating root causes of failure, inefficiency, waste and excessive costs
- Reduced insurance premiums
- Assurance that operations can be continued safely
Many plants succeed in attaining improvements by embedding CBM in the culture. Others have failed to succeed, even with a highly competent CM program.
Experience in CM and CBM
John Crane's CM services can enable you to address potential problems before they negatively impact your operations. In close collaboration with you, we will develop a reliability-based maintenance strategy for cost-effective operation and increased reliability based on your plant requirements. Learn more here.
About the author
Claire Weatheritt heads up the John Crane Asset Management Services division in Houston, TX. With 18 years of experience in machinery diagnostics and condition monitoring, she spent the first 15 years of her career in the North Sea oil rigs, working with some of the top operators to achieve best-in-class performance. She is now applying the same principles to help plants in the Gulf Coast Region improve their reliability. She is a Chartered Engineer with the Engineering Council, a Prince2 practitioner and has an MEng degree (Electrical and Mechanical Engineering) from the University of Strathclyde.
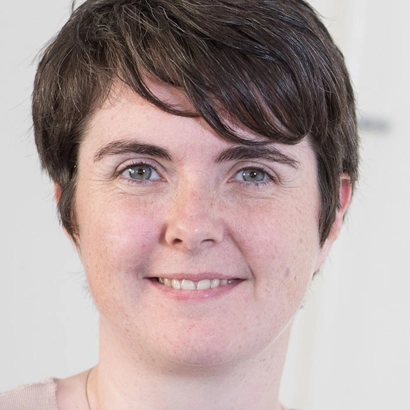